Introduction
In today’s fast-changing world, automation is becoming a key part of industries. When people think of robots, they often picture large machines working behind safety barriers, performing repetitive tasks without human interaction. These traditional industrial robots have played a major role in manufacturing for decades, handling heavy workloads with precision. However, the future of robotics is shifting towards a more collaborative approach—introducing cobots, or collaborative robots.
Cobots are different from traditional robots because they are designed to work with humans, not replace them. They can share a workspace with people, assisting in tasks while ensuring safety and efficiency. Equipped with advanced sensors, artificial intelligence, and flexible programming, cobots can handle various jobs, from assembling electronic devices to packaging products in warehouses. Their ability to adapt, learn, and work safely alongside humans makes them a game-changer for industries of all sizes.
One of the biggest reasons businesses are choosing cobots over traditional robots is their flexibility and cost-effectiveness. Unlike traditional robots, which require complex programming and dedicated spaces, cobots are easy to install and program, making them ideal even for small and medium-sized businesses. They improve productivity while reducing operational costs, allowing companies to scale their automation efforts without heavy investments.
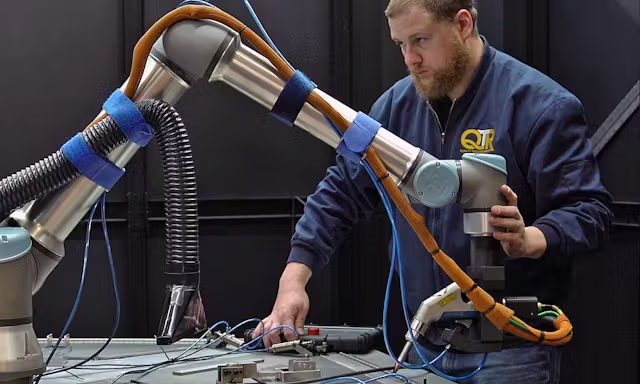
Safety is another major advantage of cobots. Unlike traditional industrial robots that require protective cages, cobots come with built-in safety features like force sensing, collision detection, and speed control. These technologies allow them to work closely with humans without causing harm. As a result, cobots are being widely adopted in industries such as manufacturing, healthcare, logistics, and even food processing.
With the increasing demand for automation, efficiency, and workplace safety, cobots are becoming the future of industrial and commercial operations. They combine the best of human skills and robotic precision, creating a smarter and more productive work environment. In this blog, we will explore how cobots work, their benefits, safety features, real-world applications, and why they are rapidly becoming a preferred choice over traditional robots.
Let’s dive into the world of collaborative robotics and see how cobots are shaping the future!
What is a Cobot?
A cobot, or collaborative robot, is a type of robot designed to work safely alongside humans in a shared workspace. Unlike traditional industrial robots, which are large, powerful, and require safety barriers, cobots are built to be flexible, user-friendly, and safe for direct human interaction.
Cobots are equipped with advanced sensors, artificial intelligence, and force-limiting technology that allow them to detect human presence and avoid collisions. This makes them ideal for workplaces where humans and robots need to collaborate on tasks like assembly, packaging, welding, and material handling.
One of the key advantages of cobots is their ease of use. Unlike traditional robots that require complex programming, cobots can be quickly trained through intuitive software or even hand-guided teaching. This means businesses don’t need highly skilled programmers to operate them, making automation more accessible to small and medium-sized companies.
Another benefit of cobots is their versatility. They can perform multiple tasks and can be easily reprogrammed for different applications, making them highly adaptable. Their lightweight and compact design allows them to fit into existing workspaces without major modifications.
Cobots are also cost-effective and energy-efficient, helping companies improve productivity while keeping operational costs low. Their growing popularity is driven by the need for safe, flexible, and efficient automation solutions in industries like manufacturing, logistics, healthcare, and even food processing.
How Does a Cobot Work?
Cobots are designed to work closely and safely with humans by using advanced technology that enables them to sense their environment, respond to inputs, and perform tasks efficiently. Unlike traditional robots, which follow rigid programming, cobots use smart sensors, artificial intelligence, and machine learning to adapt and collaborate with human workers.
Key Components of a Cobot
1. Sensors & Vision Systems – Cobots have cameras, lasers, and motion sensors that help them detect humans, objects, and obstacles in real time. This allows them to adjust movements and prevent accidents.
2. Force & Torque Sensors – These sensors allow cobots to detect pressure and resistance while working. If a cobot encounters an unexpected object (like a human hand), it can slow down or stop to prevent injury.
3. AI & Machine Learning – Cobots use artificial intelligence to analyze data and continuously improve performance. Over time, they can learn better ways to complete tasks more efficiently.
4. End Effectors (Grippers & Tools) – Depending on the task, cobots can be equipped with different tools like grippers, welding guns, or suction cups to handle materials, assemble parts, or move objects.
5. User-Friendly Programming – Cobots can be trained using simple software interfaces or hand-guided learning, where a person moves the robot’s arm to teach it a task. This makes cobots easy to use, even for non-technical workers.
6. Robotic Arm Structure – A cobot’s mechanical arm consists of joints and links that provide flexibility and a wide range of motion, allowing it to perform precise, repetitive, or delicate tasks efficiently.
How Cobots Differ from Traditional Industrial Robots?
Cobots (collaborative robots) and traditional industrial robots are both designed to automate tasks and improve efficiency. However, they differ significantly in how they operate, their level of flexibility, and their interaction with humans. While traditional robots are built for high-speed, high-precision tasks in isolated environments, cobots are designed for safe, human-friendly collaboration in shared workspaces.
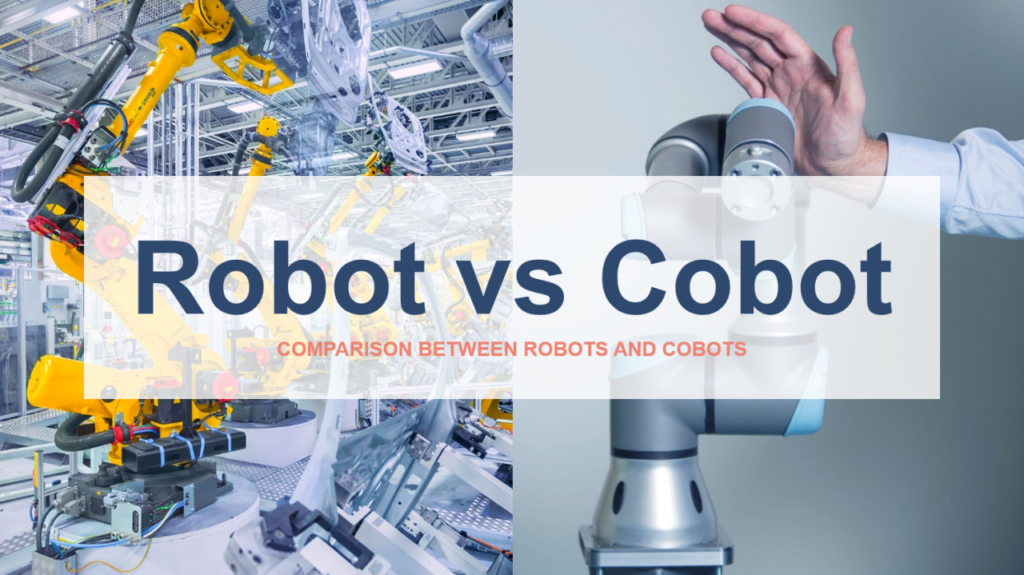
1. Human Collaboration vs. Isolation
✅ Cobots: Designed to work side by side with humans, without the need for safety cages or barriers. They can assist in tasks like assembly, packaging, and material handling, making workplaces safer and more efficient.
❌ Traditional Robots: Operate in separate, enclosed areas due to their high speed and power. They require safety fences to prevent human interaction, as they can cause injuries if not properly controlled.
2. Safety Features
✅ Cobots: Built-in sensors, force detection, and AI-driven collision avoidance ensure that cobots can detect human presence and stop or slow down if necessary. This makes them safe for workplaces where human-robot interaction is required.
❌ Traditional Robots: Rely on physical barriers and safety protocols to prevent accidents. Without these precautions, traditional robots pose a high risk of injury due to their fast and forceful movements.
3. Ease of Programming
✅ Cobots: Designed for easy programming through drag-and-drop interfaces or even hand-guided teaching, where an operator physically moves the cobot’s arm to show it how to perform a task. This makes them accessible to businesses without extensive technical expertise.
❌ Traditional Robots: Require complex programming and coding skills for setup and reprogramming. Companies often need specialized engineers to modify or update their functions, making them less flexible for frequent task changes.
4. Flexibility and Adaptability
✅ Cobots: Highly adaptable and can be quickly reprogrammed for different tasks. They are ideal for small and medium-sized businesses that need automation without long setup times.
❌ Traditional Robots: Typically fixed in one place and designed for a single, repetitive task. Changing their function requires significant reprogramming and sometimes even hardware modifications.
5. Cost and Deployment
✅ Cobots: More affordable than traditional robots, with lower setup and maintenance costs. They can be deployed in existing workspaces without major modifications, making automation accessible to small businesses.
❌ Traditional Robots: Require heavy infrastructure changes, including safety enclosures, reinforced flooring, and professional installation, leading to high upfront costs and longer deployment times.
6. Speed and Precision
✅ Cobots: Operate at moderate speeds to ensure safety but are still efficient for many industrial and service applications. They are best suited for light-duty and precision tasks that require human-like dexterity.
❌ Traditional Robots: Work at high speeds and can handle heavy loads with extreme precision. They are preferred for large-scale production lines where speed and accuracy are critical.
7. Energy Consumption
✅ Cobots: Energy-efficient, consuming less power and reducing operational costs, making them an eco-friendly automation choice.
❌ Traditional Robots: Require more power to operate, especially for high-speed and heavy-duty tasks, leading to higher energy consumption.
Which One is Right for Your Business?
- Choose a Cobot if: You need safe, flexible, and cost-effective automation that works alongside humans for small to medium-scale tasks.
- Choose a Traditional Robot if: You need high-speed, heavy-duty automation in large-scale production environments where human interaction is minimal.
Where Are Cobots Used?
Cobots, or collaborative robots, are transforming industries by making automation safer, more flexible, and easier to implement. Unlike traditional robots, which are restricted to large-scale factories, cobots can be used in small businesses, warehouses, hospitals, and even food production facilities. Here are some key industries where cobots are making an impact:
- Manufacturing & Assembly
Cobots assist in assembling products, welding, material handling, and quality inspection. They improve efficiency in industries like automotive, electronics, and aerospace, where precision and reliability are crucial. - Logistics & Warehousing
Cobots are used in warehouses for picking, packing, sorting, and palletizing goods. They work alongside human workers, reducing strain and increasing efficiency in fulfillment centers like those used by e-commerce and retail companies. - Healthcare & Pharmaceuticals
In hospitals and labs, cobots assist in patient rehabilitation, medication dispensing, and laboratory automation. They help medical staff by performing repetitive tasks, allowing healthcare professionals to focus on patient care. - Food & Beverage Industry
Cobots improve food packaging, sorting, and quality control while maintaining hygiene standards. They are used in bakeries, beverage bottling plants, and meat processing facilities to handle repetitive and precise tasks. - Small & Medium-Sized Businesses (SMEs)
Unlike traditional robots, cobots are affordable, compact, and easy to program, making them ideal for SMEs looking to improve productivity without high costs or complex setups.
With their flexibility, safety, and cost-effectiveness, cobots are rapidly becoming a key part of modern workplaces across multiple industries.
Conclusion
Cobots are changing the way industries operate by making automation more accessible, flexible, and safe. Unlike traditional industrial robots, they work alongside humans, enhancing productivity without the need for safety barriers. Their ability to adapt to different tasks makes them valuable in manufacturing, logistics, healthcare, and even small businesses.
With advancements in artificial intelligence, machine learning, and sensor technology, cobots are becoming smarter and more efficient. Businesses are increasingly adopting them to reduce costs, improve workplace safety, and increase efficiency. As industries continue to evolve, cobots will play a crucial role in shaping the future of automation.
The rise of cobots marks a shift towards a more human-friendly approach to robotics. Instead of replacing jobs, they assist workers, allowing people and machines to collaborate seamlessly. As technology progresses, cobots will continue to drive innovation and transform workplaces worldwide.